Сталь СССР (стр-4 (Прецизионные стали и сплавы - Магнитно-мягкие сплавы - Магнитотвёрдые материалы - Сплавы с особыми упругими свойствами))
Статья под цифровой редакцией подготовлена: Орловым Геннадием Викторовичем (08.11.1965) — Советским выдающимся публицистом — Историком СССР
Страницы: [01] [02] [03] [03а] [03б] [04] [04а] [04б]
Прецизионные стали и сплавы
Среди них прецизионные сплавы, благодаря высокому уровню присущих им свойств, образуют особую группу сплавов.
В эту группу входят:
- -магнитно-мягкие и магнитотвёрдые сплавы;
- -сплавы с особыми тепловыми характеристиками;
- -сплавы с особыми упругими свойствами;
- -сверхпроводящие сплавы;
- -сплавы с комплексом разнообразных физических свойств.
Промышленное производство прецизионных сплавов было впервые организовано в начале II-ой мировой войны. Подавляющее большинство прецизионных сплавов являются сплавами на основе металлов подгруппы железа: железа (Fe), кобальта (Co) и никеля (Ni). Но с ростом требований к изделиям, обладающим высоким уровнем различных свойств, получили развитие прецизионные сплавы на основе марганца (Mn), хрома (Cr), титана (Ti), ниобия (Nb) и ванадия (V), а также ряда других переходных и редкоземельных металлов.
Прецизионные сплавы находят применение в следующих областях: в машинах прикладной кибернетики; в технологических схемах преобразования энергии из одной формы в другую; в машинах, аппаратах и приборах электроники, радиотехники, космической техники и средствах связи; в устройствах и агрегатах бытовой техники: телефонные, радио-, телевизионные системы, холодильные агрегаты и другие приборы.
Магнитно-мягкие сплавы
Магнитно-мягкие стали применяют для получения магнитопроводов постоянного и переменного тока, применяемых для изготовления якорей и полюсов машин постоянного тока, роторов и статоров асинхронных двигателей, для магнитных цепей крупных электрических машин, силовых трансформаторов, аппаратов, приборов и т.д.
Общие требования, предъявляемые к магнитно-мягким материалам ‒ высокая магнитная проницаемость , низкая коэрцитивная сила HC, а для деталей магнитопроводов, работающих в переменных магнитных полях, – малые потери при перемагничивании и малые потери на вихревые токи Фуко.
Для получения минимальной коэрцитивной силы и высокой магнитной проницаемости ферромагнитный магнитно-мягкий материал должен быть чистым по примесям и неметаллическим включениям, иметь гомогенную структуру (чистый металл или твердый раствор). Даже слабый наклеп снижает магнитную проницаемость и повышает НС. Поэтому сплав должен быть полностью рекристаллизован для устранения внутренних напряжений, вызываемых наклепом.
Для характеристики явления намагничивания вводится величина I – намагниченность вещества, которая измеряется в А/м, т.е. в тех же единицах, что и напряжённость магнитного поля. Физический смысл намагниченности вещества состоит в том, что она представляет собой векторную сумму магнитных моментов частиц вещества (молекул) в единице его объёма:
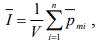
где I - намагниченность вещества, А/м; V – объём вещества, м3 ; - магнитные моменты отдельных молекул, А·м 2 .
Намагниченное вещество создаёт дополнительное магнитное поле с индукцией B' , Тл:

где µ0 – магнитная проницаемость вакуума, Гн/м. Это постоянная величина, µ0
Намагниченность вещества связана с напряжённостью магнитного поля:
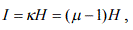
где Н – напряжённость магнитного поля электрического тока, намагничивающего ферромагнетик, А/м; µ - магнитная восприимчивость ферромагнетика; µ - относительная магнитная проницаемость ферромагнетика. Величины k и µ – безразмерные величины. Относительная магнитная проницаемость равна отношению суммарной магнитной индукции поля в веществе (B) к магнитной индукции поля в вакууме (B0=µ0H) в той же точке среды:
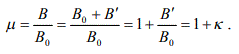
Отсюда следует, что магнитная восприимчивость ферромагнетика равна отношению дополнительной магнитной индукции к магнитной индукции поля в вакууме в той же точке среды:

Из этого следует связь между общей магнитной индукцией и напряжённостью магнитного поля:

Иногда в справочной литературе напряжённость магнитного поля приводится во внесистемных единицах – эрстедах (э). Соотношение между А/м и э следующее:
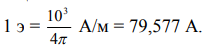
Петлёй гистерезиса называется сложная кривая зависимости магнитной индукции поля (B) или намагниченности ферромагнетика (I) от напряжённости магнитного поля (Н), создаваемого переменным синусоидальным электрическим током, в которое помещён ферромагнетик.
При снятии внешнего поля ферромагнетик остаётся намагниченным с остаточной индукцией Br . Чтобы размагнитить ферромагнетик, нужно снять остаточную индукцию, для этого нужно создать поле противоположного направления.
Напряжённость поля HC (отрезок 0-3), при которой индукция обращается в нуль, называется коэрцитивной напряжённостью или коэрцитивной силой. Значению – H (точка 4 на рисунке 1) соответствует намагниченность насыщения -IH (или индукция насыщения -BH) и, соответственно, +Н (точка 1 на рисунке 1) – намагниченность насыщения + IH (или индукция насыщения +BH). За один цикл изменения напряжённости поля от +Н до –H на перемагничивание ферромагнетика расходуется энергия, пропорциональная площади петли гистерезиса.
С учётом требований к магнитно-мягким материалам, нужно отметить, что площадь петли гистерезиса у них должна быть минимальной, т.е. петля гистерезиса должна быть достаточно узкой. Для ферромагнетиков (в частности для магнитно-мягких сталей) обычно указывается начальная относительная магнитная проницаемость (µн), когда напряжённость поля и индукция близки к нулю, и максимальное значение относительной магнитной проницаемости (µmax), так как зависимость µ=f(H) проходит через максимум.
К магнитно-мягким сплавам сейчас предъявляются всё более сложные требования: сплавы не должны подвергаться температурным воздействиям, вибрации, воздействию ионизирующих излучений (не должны стареть) и т.д. С 1950 года, когда Эльменом был изобретён пермаллой – классический магнитномягкий материал, было разработано несколько десятков магнитно-мягких сплавов, в основном на основе систем Ni-Fe, Co-Fe, Fe-Al, Fe-Si.
Старейшие магнитно-мягкие материалы – это сплавы системы Ni-Fe – пермаллои, которые наиболее полно изучены. В этой системе сплавы делят на две группы: низконикелевые (45-50% Ni) и высоконикелевые (79-83% Ni). Низконикелевые пермаллои (45Н, 50Н, 60НХС) имеют повышенную магнитную проницаемость и индукцию насыщения. Их свойства колеблются в пределах: µн = 2000 – 3000, µmax = 30000-35000 , BH = 1,0 – 1,5 Тл, HC = 8 – 16 А/м.
Высоконикелевые пермаллои (79НМ, 81НМА, 80НХС) характеризуются очень высокой магнитной проницаемостью в слабых полях при сравнительно небольшой индукции насыщения и малой коэрцитивной силе: µн = 20000-35000, µmax =(1,0-1,2)·105 , BH = 0,7 – 1,1 Тл, HC = 1,2 – 2,4 А/м. Пермаллои часто легируют Si, Mo и Сr, что приводит к уменьшению чувствительности к пластической деформации, повышению удельного электросопротивления (уменьшение потерь с вихревыми токами Фуко) и относительной магнитной проницаемости.
Индукцию насыщения BH повышают присадками в пермаллои кобальта. Зарубежные аналоги таких сплавов получили название «перминвары» (37НКДП, 35НКХСП, 33НКМСП). «П» в обозначениях сплавов означает то, что их подвергают термообработке в магнитном поле.
Нашли применение магнитно-мягкие сплавы на основе системы Co – Fe. Эти сплавы обычно легируют ванадием (50КФ). Зарубежные аналоги таких сплавов получили название «перминдюры». Положительным качеством сплавов этой системы является их способность сохранять ферромагнитные свойства при сравнительно высоких температурах. Основной недостаток этих сплавов – это низкие значения их удельного электросопротивления (r).
Ряд магнитных сплавов разработан на основе системы Fe – Al. Среди легированных железоалюминиевых сплавов наиболее широко применяются 16ЮХ и 12ЮК (легированные Cr и Co). Сплавы системы Fe – Al ферромагнитны при содержании алюминия не свыше 17%. Характерное влияние Al в этих сплавах проявляется в увеличении прочности, повышении стойкости к истиранию, росте удельного электросопротивления (r). Резервы свойств сплавов на основе системы Fe – Al могут быть увеличены при легировании хромом (Cr) и рением (Re): 16ЮИХ.
Прецизионные сплавы на основе системы Fe – Si содержат кремния не свыше 7%, так как сплавы с большим содержанием кремния непластичны и хрупки. Обычно содержание кремния в прецизионных магнитно-мягких сплавах 3 – 7%. С повышением содержания кремния увеличивается магнитная проницаемость (µ), твёрдость (HB), прочность (sв). Кроме того, в сплавах Fe – Si при ударных нагрузках, вибрациях, сжатии и колебаниях температур наблюдается большая стабильность магнитных свойств, чем в сплавах системы Ni – Fe.
Магнитотвёрдые материалы
Эти стали и сплавы применяют для изготовления постоянных магнитов. Магнитная энергия постоянного магнита тем выше, чем больше остаточная магнитная индукция Вr и коэрцитивная сила НC. Магнитная энергия пропорциональна произведению ВrНс. Поскольку Вr ограничена магнитным насыщением ферромагнетика (железа), увеличение магнитной энергии достигается повышением коэрцитивной силы НC.
Для получения высокой коэрцитивной силы стали должны иметь неравновесную структуру, обычно - мартенсит с высокой плотностью дефектов строения. Для постоянных магнитов применяю высокоуглеродистые стали с 1% С, легированные хромом (3%) ЕХЗ, а также одновременно хромом и кобальтом, ЕХ5К5, ЕХ9К15М2. Легирующие элементы повышают, главным образом, коэрцитивную силу и магнитную энергию, а также улучшают температурную и механическую стабильность постоянного магнита. Хромистые и кобальтовые стали сравнительно легко обрабатываются давлением и резанием, но обладают относительно малой магнитной энергией. Коэрцитивная сила легированных сталей составляет 4,8-12 кА/м и остаточная индукция 0,8- 1,0 Тл. Наиболее высокие магнитные свойства имеют стали ЕХ5К5, ЕХ9К15М2 после нормализации, высокого отпуска, закалки и низкого отпуска (при 100°С).
В промышленности наиболее широко применяют сплавы типа алнико (ЮНДК15, ЮН14ДК25А, ЮНДК31Т3БА, ЮНДК40Т8АА, ЮНДК35Т5БА, ЮНДК35Т5АА). Сплавы тверды, хрупки и не поддаются деформации, поэтому магниты из них изготовляют литьём.
Высокие магнитные свойства сплавы получают после нагрева до 1250- 1280 °С и последующего охлаждения (закалки) с определенной (критической) для каждого сплава скоростью охлаждения; после закалки следует отпуск при 580-600 °С.
Для создания магнитной текстуры сплавы типа алнико подвергают термомагнитной обработке: нагреву до 1300 °С и охлаждению со скоростью 0,5-5 °С/с (в зависимости от состава сплава) в магнитном поле, приложенном вдоль направления важного для магнита данной конфигурации. Затем магнит отпускают при 625 °С. После такой обработки магнитные свойства сплавов становятся анизотропными, их магнитные характеристики (Вr , НC, Br HC ) сильно возрастают в направлении приложенного магнитного поля (магнитная текстура).
Для изготовления магнитов применяют и порошковые сплавы Fe–Ni–Al ММК 1 (НС = 24 кА/м, Br = 0,6 Тл), ММК7 (Hс = 44 кА/м, Вr = 0,95 Тл), ММК11 (НС = 118 кА/м, Вr = 0,7 Тл). Эти сплавы проходят такую же термическую обработку, как и литые сплавы. Сплавы не обладают хрупкостью.
Некоторое применение нашли деформируемые сплавы 52КФА, 52КФБ и 52КФ13 (51–53% Со, 11–13% V, остальное – Fe), изготовляемые в виде проволоки диаметром 0,5–3,0 мм, полос и лент толщиной 0,2–1,3 мм. После закалки и холодной деформации сплавы подвергают отпуску при 600–620 °С. Свойства сплавов после такой обработки: 58–62 HRC, HС =28 кА/м и Вr=85 Тл (в зависимости от полуфабриката). Сплавы Fe–Ni–Аl–Nb, содержащие 8,4–9,8% Аl, 3,7– 4,2% Nb и 20–25% Ni (остальное Fe), в виде горячекатаных листов используют для изготовления малогабаритных магнитов. В промышленности используют сплавы на основе системы Fe–Со–Сr, достаточно хорошо деформируемые при прокатке. Свойства сплавов типа К23Х31С1 после термической обработки НС ~ 52,8 кА/м и Вr = 1,15 Тл.
Использование редкоземельных соединений дает возможность создавать материалы для постоянных магнитов малой массы с большой магнитной энергией ВrНс. Наиболее эффективными для этой цели являются интерметаллические соединения кобальта с легкими редкоземельными металлами, такие как SmCo5, NdCo5, PrCo5.
Сплавы с заданным коэффициентом термического расширения
Сплавы с заданным коэффициентом термического расширения составляют одну из важнейших групп прецизионных сплавов.
Тепловое расширение – это увеличение линейных размеров и объёмов тел, происходящее при увеличении их температуры. Линейное тепловое расширение характерно для твёрдых тел. Объёмное тепловое расширение характерно для твёрдых тел и жидкостей. Линейное тепловое расширение характеризуется коэффициентом a (К-1 ), а объёмное тепловое расширение – коэффициентом b (К-1 ):
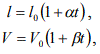
где l и V – соответственно длина и объём тела при температуре t, °С; l0 и V0 - соответственно длина и объём тела при температуре 0°С. Для твёрдого изотропного тела между коэффициентами a и b существует связь:
b = 3a .
Более точными являются формулы:
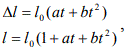
где a и b – коэффициенты, определяемые экспериментально для каждого сплава.
Коэффициент линейного расширения изменяется с изменением температурного интервала нагрева тела. Для большинства твёрдых тел a = (10-6 – 10-5 ) К-1 . Например, для чистого железа получена такая зависимость:

Аномалии термического расширения наблюдаются во многих бинарных сплавах. Существует две группы сплавов с заданным коэффициентом термического расширения: сплавы с аномально низким значением коэффициентом термического расширения (a »10-7 К-1 ); сплавы с аномально высоким значением коэффициентом термического расширения. В основе создания той или иной группы сплавов положен принцип экспериментального поиска аномалий коэффициента термического расширения в зависимости от химического состава сплава (рисунок 3.1).
Рисунок 3.1 - Зависимость коэффициента термического расширения от состава для некоторых бинарных сплавов.
В зависимости от назначения сплавы с аномалией коэффициента термического расширения должны обладать также хорошими механическими свойствами. Их используют для изготовления измерительных инструментов, которые не должны изменять свои размеры в определённом интервале температур, для изготовления многочисленных устройств вакуумной техники и пр.
Наибольшее применение получили сплавы на основе системы Fe – Ni. Аномалия коэффициента термического расширения сплавов на основе системы Fe – Ni имеет ферромагнитную природу: он минимален лишь в очень узком интервале содержания Ni, где он почти на порядок меньше, чем у чистых железа и никеля.
Среди бинарных железоникелевых сплавов с низким коэффициентом линейного расширения известен и всесторонне изучен сплав инвар. Его аналог – это сплав 36Н. При помощи специальной термомеханической обработки можно ещё более понизить и стабилизировать характерный для инвара весьма низкий коэффициент термического расширения.
Сплав суперинвар (32НКД) имеет ещё более низкий, чем у инвара коэффициент термического расширения и содержит небольшое количество легирующих элементов Co и Cu. Отличительной особенностью сплава 35НКТ является сравнительно высокие механические свойства, приобретаемые в результате дисперсионного твердения. Основные характеристики сплавов с низким и заданным коэффициентами температурного расширения приведены (в таблице ниже).
Основные характеристики сплавов с низким и заданным коэффициентами температурного расширения |
Сплав |
aср.·105 , К-1 |
Точка Кюри, °С |
r, мкОм-м |
Е, МПа |
sв, МПа |
d,% |
НС, А/м |
Сплав с низким коэффициентом температурного расширения |
36Н |
1,5 (20 — 100 °С) |
220 |
0,82 |
14800 |
447 |
45 |
12,7 |
32НКД |
1 (20 — 100 °С) |
220 |
0,78 |
14100 |
451 |
41 |
12,7 |
35НКТ |
3,5 (20 — 100 °С) |
210 |
0,85 |
— |
1110 |
17,5 |
15,1 |
Сплав с заданным коэффициентом температурного расширения |
47НД |
9,5 (20 — 300 °С) |
450 |
0,45 |
14700 |
510 |
40 |
22,3 |
47НХР |
9,0 (20 — 300 °С) |
340 |
0,9 |
13700 |
510 |
40 |
19,9 |
18ХМТФ, 18ХТФ |
11,3 (20 — 500 °С) |
580 |
0,62 |
22000 |
490 |
28 |
127,3 |
Повсеместное признание получил сплав ковар (29НК). Этот сплав имеет низкий коэффициент температурного расширения в широком интервале положительных и отрицательных температур. Образующиеся в процессе пайки на поверхности этого сплава оксиды легко и полностью растворяются в определённых сортах тугоплавких стёкол, что является предпосылкой получения плотного и прочного спая.
На практике для сплавов, подобных 29НК, требуется ещё больше уменьшить значение коэффициента термического расширения или увеличить температуру Кюри, то есть расширить температурную область использования сплава. Для удовлетворения подобных требований разработаны две модификации сплава 29НК: 30НКД, 33НК.
К сплавам с заданным коэффициентом температурного расширения следует отнести и сплавы с особо высоким коэффициентом температурного расширения. Такие сплавы созданы на основе Mn. Из числа промышленных сплавов на основе Mn следует выделить сплав 75ГНД: он успешно применяется в производстве термостатических биметаллов в качестве их активной составляющей. Сплав с низким коэффициентом температурного расширения используется для изготовления пассивной составляющей. Коэффициент температурного расширения сплава 75ГНД в несколько десятков раз больше, чем у сплавов, применяемых для изготовления пассивной составляющей.
Сплавы с особыми упругими свойствами
Основное свойство, которыми должны обладать пружинные стали и сплавы со специальными упругими свойствами – высокое сопротивление малым пластическим деформациям в условиях кратковременного (предел упругости, sупр.) и длительного (релаксационная стойкость) нагружения.
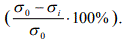
Эти свойства зависят от состава и структуры этих материалов и внешних условий: температуры, коррозионной активности внешней среды и др.
Следует особо подчеркнуть, что сопротивление малым пластическим деформациям определяет весь комплекс свойств пружинных сталей и сплавов. Теоретическими исследованиями установлено, что для достижения высокого сопротивления малым пластическим деформациям необходимо обеспечить равномерное распределение дислокаций при их высокой плотности, полном их закреплении, чтобы в максимальной степени затормозить развитие самых начальных стадий пластической деформации. Достижение данного структурного состояния обеспечивается разными механизмами упрочнения или их одновременным использованием.
Наиболее широко используются механизмы упрочнения, основанные на протекании мартенситного превращения (y→a), на выделении избыточной высокодисперсной фазы, на внутрифазовых превращениях с образованием ближнего упорядочения или ближнего расслоения, на использовании деформационного наклёпа.
Эти материалы классифицируют по основным способам упрочнения и назначению. По основным способам упрочнения различают:
- - сплавы, упрочняемые холодной пластической деформацией и последующим низкотемпературным нагревом [стали перлитного класса (0,4-1,2% С);
- - стали аустенитного класса; сплавы меди (латуни и бронзы)];
- - cплавы, упрочняемые в результате мартенситного превращения y→a (мартенситно-стареющие углеродистые и легированные стали);
- - сплавы, упрочняемые в результате дисперсного твердения (старения) – это сплавы на основе систем Fe-Ni, Fe-Ni-Cr, Co-Ni-Cr, Ni-Cr и др., с добавками главным образом Ti, Al или Nb, образующих упрочняющие фазы, выделяющиеся в дисперсной форме при последующем старении или отпуске.
По назначению различают пружинные стали и сплавы общего назначения и специального назначения. Пружинные стали общего назначения должны обладать высоким сопротивлением малым пластическим деформациям (предел упругости, sупр.), высоким пределам прочности (sв) при достаточной вязкости (KCV, KCU),а также повышенной усталостной прочностью (s-1) и релаксационной стойкостью (sполз.¯); 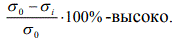
К ним относятся:
- - углеродистые стали перлитного класса (65, У9А, У12А);
- - легированные стали перлитного класса (60Г, 70С3А, 50ХФ);
- - стали мартенситного класса (20Х13).
Пружинные стали и сплавы специального назначения кроме вышеперечисленных качеств должны иметь повышенная коррозионная стойкость, немагнитность, малое удельное электросопротивление, независимость модуля упругости от температуры.
Стали и сплавы, относящиеся к этому классу, делятся на следующие группы:
- коррозионно-стойкие;
- немагнитные; |
|
- элинварные |
 |
- теплостойкие.
Эти стали и сплавы выполняются на основе систем Fe-Ni-Cr, Ni-Cr, CoNi-Cr-Mo, которые представляют собой стали мартенситного класса (20Х13), аустенитного класса (12Х18Н9Т), аустенитно-мартенситного класса (09Х15Н8Ю), мартенситно-стареющие стали (03Х12Н10Д2Т), аустенитные сплавы.
Применение сплавов со специальными упругими свойствами непрерывно расширяется. Их выдающиеся свойства: высокий модуль упругости (Е);
- малый температурный коэффициент модуля упругости |
 |
- высокая прочность (sв ,HB); |
|
- высокая коррозионная устойчивость; |
|
- теплостойкость, немагнитность (µ»1). |
|
Основой таких сплавов являются железо, никель и кобальт.
Железоникелевые сплавы имеют минимальное значение модуля упругости при 36% Ni и в то же время наибольший температурный коэффициент . Оптимальное сочетание модуля упругости и температурного коэффициента достигается на сплавах с 30-45% Ni. С помощью дополнительного легирования этой основы можно изменять обе эти характеристики в заданных пределах. Эти элементы должны упрочнять твёрдый раствор. Сплавы с минимальным температурным коэффициентом называются элинварами (30-45% Ni и 6-13% Cr). Сплав 35 НХМВ идёт на изготовление волосков – деталей часового механизма. Сплав 42НХТЮА – аналог зарубежного сплава ниспен; этот сплав, а также 44НХТЮ, замечателен тем, что изменение температуры не изменяет частоту колебаний изделий из этих материалов.
Сплавы системы Сo-Cr-Ni обладают непревзойдёнными упругими и прочностными свойствами (40КХНМ, 40КНХМВ, 40КНХМВТЮ и др.). Упругие элементы, изготавливаемые из этих сплавов, отличаются высокой эксплуатационной долговечностью. Так, пружина из сплава 40КХНМ способна выдерживать циклические нагрузки в четыре раза больше, чем нагрузки, выдерживаемые пружиной из углеродистой стали. Теплостойкость сплавов граничит с жаропрочностью и жаростойкостью: упругие элементы, изготавливаемые из этих сплавов, могут применяться в устройствах с температурой до 500°С. Легирование этих сплавов увеличивает их прочность. Установлено, что добавка рения Re к сплаву 40 КХНМ повышает твёрдость на 10-12%.
[03б] <<< [04] >>> [04а]
Источник: http://ussr-cccp.moy.su/index/promyshlennost_sssr/0-43 |